The Big Rocket Showdown: Falcon 9 vs Neutron
A discussion of the different design philosophies and strategies of SpaceX and Rocket Lab
Let us do a comparison between the current king of the rocket launch industry, Falcon 9 manufactured by SpaceX and the upcoming contender Neutron being designed by Rocket Lab, a company originating in New Zealand. While you may not have heard about Rocket Lab, it is probably the most successful and innovative rocket launching company besides SpaceX. They were the first to make fully 3D-printed rocket engines and launch a rocket made from carbon fiber composite into orbit.
I could go on about all the cool stuff Rocket Lab has done, but the bottom line is that this is a company with a strong track record. They have been busy developing Neutron for a year now and recently put their new Archimedes engine on display. Ten Archimedes engines will power the Neutron rocket: nine for the first stage and one for the second stage. Rocket Lab has also shown the completion of tooling and moulds to build the rocket. When a company has created moulds and tooling for a rocket, it means they are confident about having finalized all key design work.
This new milestone in development allows us to start making some comparisons with Falcon 9 in terms of design choices, specifications, and performance. More specifically, I want to cover the following topics in this article:
Specifications – How do they compare in size, weight, power, and payload delivery capacity?
Engines – How does the Merlin engine of the Falcon 9 compare with the new Archimedes engines?
Material choice – One rocket is made from aluminum, while the other is made from carbon fiber composite. What are the tradeoffs?
Rocket shape – Why do Neutron and Falcon 9 have such different geometries?
Reuse – What makes the Rocket Lab approach to reuse so different from that of SpaceX?
Before jumping in and comparing Neutron to Falcon 9 it is important to keep in mind that Falcon 9 has been refined and optimized over many years. Thus, we can assume that there is plenty of scope for improvement on the first version of Neutron released. For instance, the current Falcon 9 rocket use the Merlin 1D rocket engine. It is a refinement of the previous Merlin 1C engine. The Merlin 1C boasted 420 kilo Newtons (kN) of thrust, while the currently used Merlin 1D doubled that to 854 kN. That radical improved allowed SpaceX to stretch the Falcon 9 rocket from 47.8 meters to its current 70-meter length, which resulted in the mass of the rocket growing from 333 tons to 549 tons.
You need roughly, 5490 kN to lift 549 tons off the ground. The nine Merlin 1C engines on the Falcon 9 v1.0 only gave a combined force of, 4940 kN. Thus, without improving the power of the Merlin engines, it would not have been possible to lift the current Falcon 9 off the ground.
Rocket Specifications and Capabilities
Rockets come in many shapes and sizes. Some send only a few hundred kilograms into orbit, while others send several tons. It is useful to get a sense of where Falcon 9 and Neutron fit in the rocket landscape.
Thus, I have made a diagram below showing relative size of some of the most widely used rockets in the industry. These rockets could be classified as medium lift launch vehicles. It refers to rockets capable of putting 2 – 20 tons of payload into orbit.
The leftmost rocket is Ariane 6 which is being developed by the European Space Agency to replace Ariane 5. The Ariane rockets have been popular rockets for launching commercial satellites into orbit. Next follows Soyuz-2 which is the workhorse of Russian Roscosmos. It is an evolution of the Soyuz, which first got used in the 1950s. No rocket has had more launches than Soyuz and its derivatives. Before Falcon 9 this rocket dominated the commercial space industry. Both American and Russian astronauts rode on this rocket to the International Space Station (ISS).

For height comparison, let us sandwich in Neutron between the first version of Falcon 9 that was launched and the current Block 5 version.
While both versions of Falcon 9 are taller than Neutron, you will see that on other metrics such as mass, Neutron is typically located somewhere between the two Falcon 9s. Another interesting detail is that despite Ariane 6 looking massive, it is actually slightly lighter than Falcon 9. And Soyuz is not quite as light as you might have imagined from looking at its size.
What is the explanation for these apparent contradictions? In relative terms, rockets have thinner metal walls than soda cans. Thus, the fuel and oxidizer is what constitutes most of the mass. Both Falcon 9 and Soyuz-2 use Kerosene fuel (RP-1) at all stages. Kerosene is very dense. Ariane uses Hydrogen fuel, which is very low density. That means much larger fuel tanks are required to hold the same amount of fuel.
The payload each rocket can send to orbit matches their total mass somewhat, although there are some outliers. Most notable is Ariane 62. The key reason is that these rockets use strap-on boosters with solid rocket fuel. For old space companies such as Arianespace and United Launch Alliance (ULA) which make these rockets, that is a very common strategy. Thus, Ariane with two solid fuel rocket boosters can deliver 10.35 tons into low earth orbit (LEO) while adding another pair of boosters doubles that to 21.65 tons. On the other hand, Ariane 6 with four boosters comes in at 860 tons, making it significantly heavier than any of the other rockets.
Yet, the performance of Ariane 6 still looks underwhelming at first glance. You would think it has low thrust, but the bar chart below shows that it has a pretty good kick upon launch. So, what explains the discrepancy? The reason is that Ariane is better optimized towards delivering payloads into higher orbits. For geostationary orbit (GTO) Ariane puts heavier payloads into orbit than Falcon 9.
Falcon 9 and Neutron are substantially different from these other rockets because no strap-on boosters are used. Why not? Because solid fuel rockets are like the blackpowder rockets you use to celebrate New Year: You ignite them and they go. There is no opportunity to control them with any precision, unlike a liquid fuel engine with a turbo-pump. Thus, you cannot land these boosters after use the way SpaceX does with Falcon 9 and Falcon Heavy.
Now that you got some idea of what kind of rockets Neutron and Falcon 9 are most comparable to, let's focus our attention on their differences. Notice that both in terms of mass and payload, the Neutron rocket sits somewhere between the Falcon 9 v1.0 and the current Falcon 9 Block 5 variant.
It is normal to aim for good margins first so that you get successful rocket launches, and then begin optimizations and improvements later. The design of Neutron makes upgrades harder. Straight cylinder rockets like Falcon 9 can be upgraded easily by stretching them. Neutron, in contrast, cannot as easily be stretched as it is tapered. The base is 7 meters in diameter, while the nose cone is 5 meters in diameter.
Merlin 1D vs. Archimedes
The first announced design of Neutron a year ago specified that Neutron would use seven engines in the first stage. Interestingly, the revised design will use the same configuration as Falcon 9: Nine engines in the first stage and one in the second stage.
Incidentally, it is the exact same configuration used by the Electron rocket currently used by Rocket Lab. It is seen as a practical choice because the second stage doesn't need more than 1/9th the power of the first stage. It is also practical for reusability because need to throttle back considerably to land a booster with propulsion. Too much thrust and your booster stage will shoot upwards instead of merely slowing the descent towards the ground.
It is quite hard to throttle rocket engines down to an arbitrary low level. It is easier to shut engines off completely. When the Falcon 9 booster lands, it shuts down all engines except one and throttles down to 57 percent of max thrust. Yet even that isn't low enough to get a controlled landing. Instead, the Falcon 9 booster famously lands with a hover slam. Basically, it fires an engine right before it slams into the ground.
It is interesting to see how common this rocket engine configuration is becoming because the previous generation of Western rockets such as Atlas, Ariane, the Space Shuttle, Delta and Saturn V all used relatively few and large engines. They also used entirely different engines and fuel for each stage, while the thinking of current generation rocket companies is to be able to reuse as many components and technology as possible for each stage to simplify and keep costs down.
Engine Thrust and Efficiency Compared
Enough about engine configuration. Let us zoom in on a single engine and compare them. In terms of raw power, the Archimedes sits between the old Merlin 1C and the current Merlin 1D. This gives Falcon 9 an advantage in the first stage. Rockets want to get off the ground as quickly as possible to avoid wasting fuel fighting gravity.
But when looking at propellant efficient (Isp) the tables turn. Here, Archimedes with a specific impulse of 329 seconds beats Merlin 1D with only 282 seconds of specific impulse. That means the same amount of fuel can provide thrust for a longer time on a Neutron rocket than a Falcon 9. It is 17 percent more propellant efficient. That advantage grows in vacuum to 18 percent.
What are the practical consequences of this difference? It will matter most for the second stage, allowing it to go higher. That matters, especially if you want to get payloads into higher orbits. That advantage is very clear with the Ariane rocket. The stats I showed in this article for Ariane makes it look like a crappy rocket because it can deliver much less payload to low Earth orbit than a Falcon 9 despite being a rocket of very similar size.
But Ariane has a Hydrogen engine as its second stage, which has a specific impulse of 318 seconds at sea level. However, once in vacuum, it has an Isp of a crazy 432 seconds. Here, Falcon can only reach 311 seconds. In other words, Ariane has a 39 percent advantage at higher orbits. That helps explain why Ariane beats Falcon 9 at delivering cargo to high orbits.
Suitability for Reuse
Engines burning methane are much better suited for reuse than engines burning kerosene because methane burns cleanly, while kerosene cause soot to buildup in the engines. We refer to this as coking. Founder of Rocket Lab, Peter Beck, humorously said you can eat your lunch out of the engine bells of the Archimedes engine after they have flown. That means methane engines require significantly less maintenance. There is no need for extensive cleaning of the engines after they have flown.
Gas Generator vs. Oxygen Rich Staged Combustion Cycle
When describing engines it is normal to categorize them by what we call power cycle which describe a thermodynamic cycle for an engine. That may sound like a bunch of gobbledygook, but basically refers to the steps involved when an engine operates. It says something about how heath is transferred and used to do work. The gasoline engine in your car for instance typically follows the Otto cycle, while a diesel engine use the Diesel cycle. Steam turbines use the Rankine cycle.
We can describe rocket engines with power cycles as well. Two common ones are the gas generator cycle and the staged combustion cycle. I have an article discussing this in more detail:
Gas generator engines are simple and cheap to make. Staged combustion engines come in several variants, but I will only talk about oxygen-rich staged combustion cycle here. These engines are much harder and expensive to make. However, it all depends on the performance you are aiming for. The Merlin 1D engine is a gas generator, which makes it a relatively simple engine. The Archimedes engine in contrast use a staged combustion cycle running oxygen-rich in what we call the pre-burnerwhich drives the turbo pump of the engine.
A key difference in design is that Archimedes is a low-performance version of a high-performance cycle, while Merlin 1D is a high-performance version of a low-performance cycle.
The benefit of the Rocket Lab approach is that they get much larger tolerances on their engines. If you want to maximize reuse, you don't want engines to run close to their breaking point but with fat margins.
Aluminium vs. Carbon Composite Rockets
Falcon 9 is built using aluminum, which is the most popular and common material in the space industry to build rockets. Rocket Lab is going a radically different route by building Neutron using carbon fiber composite. That is an unusual choice, but a very sensible one for Rocket Lab. They already have extensive experience building rockets out of carbon fiber; that is what their existing Electron rocket is made from. New Zealand, where Rocket Lab originates, has a strong expertise in working with composite materials thanks to the yacht industry. Peter Beck himself worked extensively with composites before founding Rocket Lab.
If anyone can pull off building a large rocket out of carbon fiber composites, it is Rocket Lab. Another question is whether one should use carbon fiber. Let us look at the pros and cons.
Advantages of making a Rocket from Aluminum
Metal is relatively easy to work with. You can bend, roll, melt, hammer, stretch, stamp and weld it. Aluminum gives you most of these advantages while also giving better strength to weight ration than steel, allowing you to build lighter rockets.
For SpaceX, it is a big advantage because their approach to developing rockets is through a hardware-rich iterative approach. More specifically, almost anything they develop is based on making numerous physical prototypes which they test out. After each test, they learn something and use that to refine their design.
Metal is well suited for rapid experimentation as you do not need to build tools and moulds like with composite materials.
Advantages of Carbon Fiber Composites
Carbon fiber composite is a material composed of layers of carbon fiber cloth soaked in resin to get hard. The idea is that you combine materials with different properties into a new composite material which superior properties. Think about concrete reinforced with steel, or boats made with glass fiber composites.
Carbon fiber is kind of a wonder material, as you can achieve the same strength as steel with 1/5th the weight. You can get the same strength as aluminum at 1/4th the weight.
The question is: How much does mass matter to rockets? The Tsiolkovsky rocket equation helps us answer that question. It tells us that in space, our ability to get from one planetary orbit to another is dependent alone on:
Propellant efficiency of the rocket engines. What we call specific impulse (Isp).
Mass of rocket with fuel (wet mass).
Mass of rocket without fuel (dry mass).
That is it! It doesn't really matter how big your rocket is or how powerful your engines are. Powerful engines matter when you try to get off the surface of a planet and fight gravity. On the other hand, when you accelerate perpendicular to the force of gravity, what matters is: How fuel efficient your engines are and how light the structure of your rocket is relative to the propellant (fuel and liquid oxygen) it holds.
I did a few calculations to explore how much material choice matters. I compared the output of the rocket equation for a regular Falcon 9 with a Falcon 9 with 1/4th the dry mass. That gave 44 percent better performance. I compared with the effect of replacing the Merlin engines with the new fancy Raptor 2 engines that SpaceX have developed. That only gave a 16 percent improvement. If you are curious and know Julia code, you can see my implementation here:
const g0 = 9.807 # acceleration of gravity on Eart
function velocity(drymass, propellant, Isp)
wetmass = drymass+propellant
massratio = wetmass/drymass
return Isp*g0*log(massratio)
end
In the Julia REPL environment, I used this function to perform the following calculations (just ignore this code if it doesn't make any sense):
julia> velocity(26/4, 523, 282) / velocity(26, 523, 282)
1.4426649973915697
julia> velocity(26, 523, 327) / velocity(26, 523, 282)
1.1595744680851063
Thanks to the material choice, the Neutron rocket gets similar Thrust to Weight (TWR) as the current Falcon 9, despite having engines with 14 percent less thrust. TWR is important as it says something about a rockets' ability to get off the ground quickly. If the TWR is 1.0 it means the thrust is equally strong as the pull of gravity and so you are getting nowhere. Thus, in order to ascend, you need a TWR greater than 1.0. A higher TWR means the rocket accelerates faster.
The effect of lighter material becomes more stark if you play with the rocket equation to see how much you can reduce the propellant. Without payload, you require only 1/4th as much propellant to get the same performance as when using aluminum. But that means you only require 1/4th as large tank. But this means you require only 1/8th as much propellant, which again means you only require a tank 1/8th as large, but that means you require even less propellant. You get this crazy downward spiral, reducing the rocket size. What stops it from going further down is that you need to deliver a payload. The larger the payload, the less dramatic this downward spiral becomes.
But Isn't Carbon Fiber Expensive and Slow to Work With?
SpaceX has helped perpetuate the myth that Carbon fiber is expensive and slow to work with ever since they abandoned their attempts to make a Starship out of carbon fiber composite. Here there is a need for clarification: Experimentation and iteration is slow with carbon fiber, but not manufacturing.
The problem with carbon fiber composite is that you need to build tools and moulds. That takes time and is expensive. However, once you got those made, manufacturing of carbon fiber shapes is very fast. Yes, the material is pricier than aluminum, but you also require far less of it.
The reputation of Carbon fiber as expensive is primarily from the previous extensive need for manual labour to create carbon fiber composite parts. But today there are highly automated robot systems which can create large carbon fiber composite parts rapidly. This technique called Automated Fibre Placement (AFP) is widely used to make parts for airplanes.
In many ways, carbon fiber is part of the 3D-printing revolution. More generalized 3D-printing is what we call additive manufacturing (AM), while Falcon 9 is made using traditional subtractive manufacturing. In the first case, you build a structure by adding material one small piece or layer at a time. Subtractive manufacturing in contrast involves cutting out, drilling and machining parts and components from bigger parts. It is like the difference between sculpting with clay and with rock. You add clay to create a sculpture, while a stone sculpturer chisels away rock to form their sculpture.
Additive manufacturing is lauded for wasting less material. It is a process to a large degree based on using more advance robot systems. 3D printing relies on a robot arm to precisely deposit small droplets of material. Automated Fibre Placement has also emerged as advanced robotics have evolved. It is not without reason that composite materials are seeing increased usage in all industries. Here I think Rocket Lab has a huge advantage over all their competitors. They got in early and gained valuable experience with what is the material of the future.
In the next section, where I discuss the unique geometry of the Neutron, it will become more clear why carbon fibre is such a tremendous advantage.
Long and Thin vs. Short and Stubby
I explained the downward spiral with carbon fiber composite in terms of tank size. That means the second stage of the Neutron can be shrunk a lot, while still delivering the same performance. This effect gets further amplified by the fact that the Archimedes methane/LOX engine gives much better specific impulse than Merlin 1D in vacuum.
A shrunk second stage opens the possibility to place the second stage inside the first stage instead of stacking it. Why is that useful? Because then the payload fairing can be attached to the first stage. When the second stage is fired up, the Neutron can just open the fairing and let it out. Afterward, it can close the fairing and return to Earth for landing. That allows us to bring the fairing back to Earth, which saves money and time. Fairings are quite expensive. The Fairings on the Falcon 9 for instance cost around $6 million, which is three times more than it costs to build a whole Electron rocket and about the same as carrying out a full launch to orbit for Electron.
To make all of this work, Neutron pull another trick: The second stage is not stacked, but hung inside the 1st stage. That means the structure of the 2nd stage does not need to be strong enough to withstand the compression from the payload, only to be strong enough to handle the tension from the rocket engine hung underneath. This strategy allows one to shrink the second stage further, which makes placing it in the first stage work even better.
However, it has a secondary effect: The material needs for the second stage are reduced. That means the second stage becomes much cheaper and faster to make than the Falcon 9 second stage.
I have yet to explain why the Neutron rocket is short and stubby rather than long and thin like the Falcon 9. There is a actually considerable difference between the two rockets. The Falcon 9 has a diameter of only 3.7 meters, while Neutron has a diameter of a whole 7 meters. That is actually as wide as the New Glenn rocket being developed by Blue Origin, which is a significantly larger rocket.
The area at the bottom of Neutron is a full 3.6 times larger than that of the Falcon 9. The rocket taper at the top leading to the fairing being 5 meters in diameter, slightly smaller than the fairing of the Falcon 9.
If you are sending a rocket up in the air, you want it to be thin to pierce through the air and receive less air resistance. The Falcon 9 shape makes sense from that perspective. However, that is not a good shape for landing. The shape of the Neutron rocket in contrast is as much optimized for landing as it is for launching. It has a tapered top to get less air resistance when going up. To get more air resistance when going down, it has a wider base. Peter Beck has compared the Neutron rocket to an umbrella. An umbrella is wide and light, which means it falls through the air slowly.
Thanks to carbon fiber composite, Neutron will be up to four times lighter than Falcon 9 when returning for landing, while the base is 3.6 times larger in area. That means Neutron is significantly more capable of slowing down when returning without burning any fuel. It also means the carbon fiber body of the Neutron rocket will not get exposed to high temperatures. Keep in mind that carbon fiber composite cannot tackle high temperatures as well as metals.
Falcon 9 vs. Neutron Reuse Strategies
The Neutron rocket, like Falcon 9, doesn't reuse its second stage. Both rockets have expendable second stages. How is Neutron any improvement on the Falcon 9 then? And how will it be able to compete with Starship, which is designed to reuse both stages?
What if I tell you that you have been grossly mislead about what drives the cost of rocket launches? Companies like SpaceX and its leader Elon Musk has naturally had a financial interest in hyping up the wonders of reusable rocket. Yes, reuse matters, but not quite in the way you imagine. The idea that many people have is that the primary cost of launching a rocket is in building the rocket itself. Many think that with fully reusable rockets, the cost of launching is reduced to the cost of refueling.
Here is a simple fact that challenges that narrative: When Rocket Lab launches an Electron rocket, it costs about 6 million dollars. How much do you think it costs to build that rocket? Only $2 million! What are the remaining $4 million for? The remained is for operations and services related to the launch.
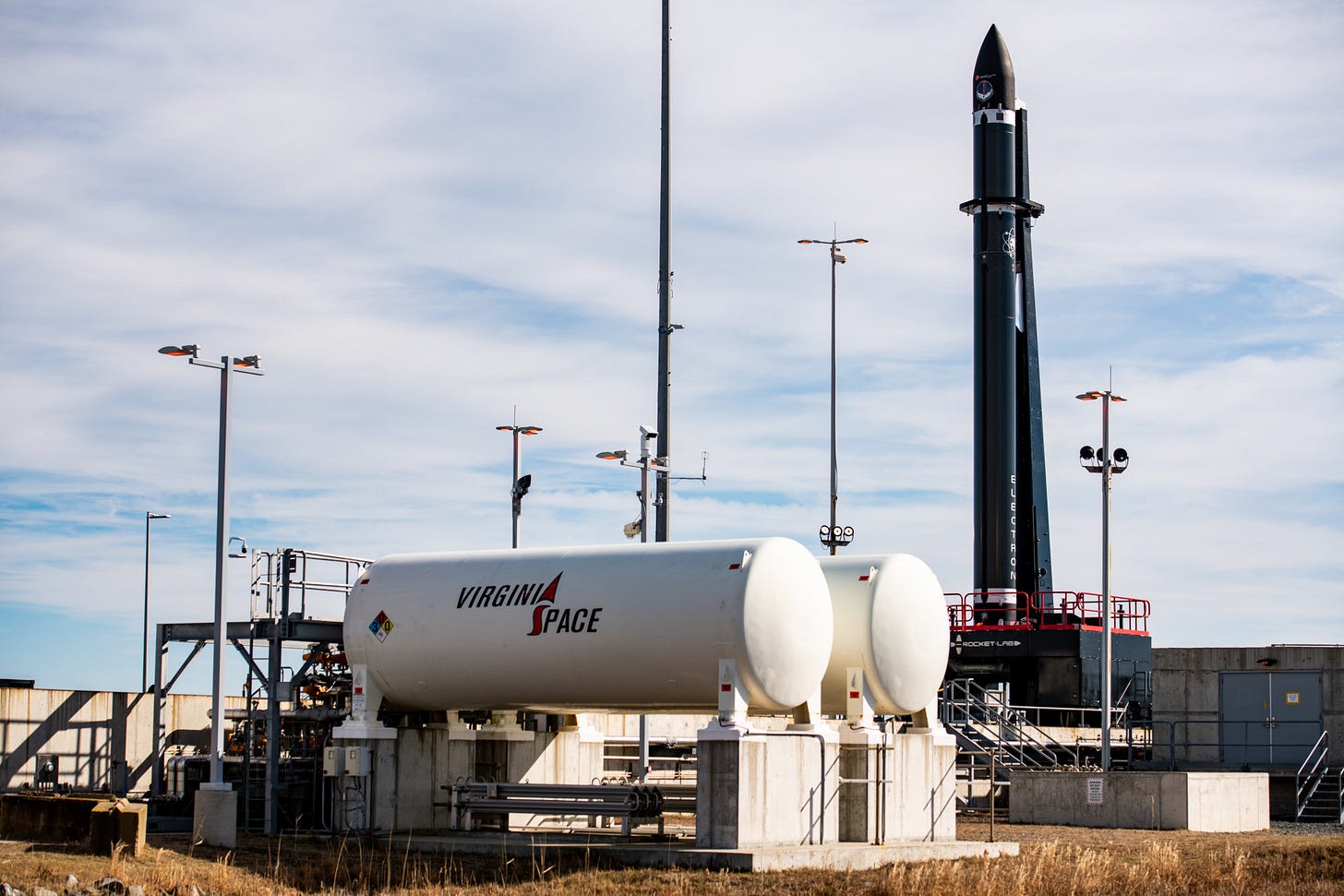
In other words, only 1/3 of the cost comes from building the rocket. Fully reusing an Electron rocket can thus only save 1/3 of the cost. Operating a launch pad is expensive.
Think about it this way: Why was Tesla in the red for so many years, despite making money on every car they sold? Because the cost of running a car company was higher than the total profits from all the cars sold. Whether you run a rocket company or a car company, you have massive fixed costs which have to be amortized across every car sold or every rocket launched. That is why making a profit is all about volume. If you have enough volume, you can pay your fixed costs.
The Space Shuttle was a reused vehicle, but it still ended up costing $1.5 billion per launch! The cost for just a launch was $450 million, according to NASA, but that doesn't consider the cost of building the shuttles and all other fixed costs. Thus, the inability to achieve frequent launches is what drove up the average cost per launch.
The primary reason Rocket Lab changed their decision to attempt reuse of the Electron Rocket was not to save production costs, but to get more frequent launches. They simply could not build rockets fast enough to keep up the launch frequency.
Thus, when designing and developing the Neutron rocket, reuse has only been one part of the overall cost-cutting strategy. Equally important, if not more important, is a strategy to reduce infrastructure costs and increase launch frequency. To achieve that, Neutron is being designed for reuse within 24 hours of landing. It also doesn't require a launch tower. All that is needed is a plain flat pad. Rocket Lab is optimizing for return to pad rather than landing on a drone ship. Peter Beck remarked in interviews about how much it costs to maintain marine infrastructure such as drone ship.
SpaceX has followed a different strategy, which is primarily focused on achieving as high reuse of the rocket as possible. You can see that in how Falcon 9 requires a more complex launch infrastructure. Starship, currently in development, follows the same trend. You can see in the picture below how it requires a large, complex launch tower.
Falcon 9 is not as much cheaper relative to other expendable rockets as you might think. The plot below shows cost breakdowns for different rocket launches. For each rocket, I have added the category other as a bucket term for profits and other expenses. You can see from this bar chart that a reused Falcon 9 actually costs more than making a Russian Soyuz rocket. It has been estimated that a Soyuz rocket only costs $12 million to make. That is less than the $15 million it costs to make Falcon 9 with a recycled booster stage.
If the Soyuz cost breakdown given by Gregory Shashkoff is correct, then the cost of the Soyuz rocket is only 26% of the total launch cost. The rest is shipping it, logistics, fueling, launch services, crew preparation, tracking, the spacecraft put into orbit, search, and rescue landing services.
In other words, expendable rockets are not quite as bad as you might think. Remember, a key reason that SpaceX started outcompeting other companies is that the Falcon 9 itself is cheaper to build. Long before SpaceX reused the booster stage, they already sold launches much cheaper than the competition.
How Neutron Beats Falcon 9
I have seen a couple of articles and people dismiss Neutron because it is a rocket without second stage reuse and which pushes less payload into orbit than Falcon 9. In their mind, Neutron must then be a lesser me-too version of the Falcon 9 rocket. Nothing could be further from the truth. Let me summarize the points I have covered in this article to put in one place all the advantages the Neutron rocket will bring over Falcon 9:
Payload capacity and thrust may look worse than the current Falcon 9, but keep in mind that Falcon 9 has undergone numerous improvement. The current specs for Neutron would soundly beat the original Falcon 9 v1.0.
The second stage of Neutron will be much cheaper to make than the Falcon 9 second stage, thanks to the need for less propellant and structural strength.
Simple and full recovery of payload fairing, by keeping them attached to the first stage.
Quicker turnaround time thanks to the Archimedes methane engines which require no cleaning between launches, unlike the Merlin kerosene engines.
Fixed landing legs. The broad base means you don't need to expand and contract legs for takeoff or landing. One more thing that cannot fail when landing the rocket.
No need for a launch tower, reducing infrastructure costs.
More fuel-efficient engines and lighter second stage, improving ability to deliver payload to higher orbits.
Better designed for landing. Broader base and engines which can throttle down further. A Falcon 9 style hover-slam is harder to get right and riskier.
Doesn't Starship Make Neutron Obsolete?
A discussion of Neutron vs. Starship deserves its own article, so I will only touch upon the question briefly here. The assumption that Starship will be cheaper than Neutron to launch rests on the false assumption that the cost of launching rockets is primarily building the rockets. However, as I have shown, that is often only a fraction of the total cost of launching a rocket. Fixed infrastructure and operations costs tend to dominate.
Yes, Starship will save more money on reuse than Neutron, but it will also have much more expensive infrastructure to support it. Neutron is specifically designed to have low infrastructure costs and fast turn-around.
Both rockets are designed with entirely different goals. Elon Musk created Starship primarily to colonize Mars. Finding a way to make Starship financially viable came afterward. Neutron in contrast is a response to market demand. It is made to launch satellites into orbit and possibly do manned missions to the International Space Station (ISS).
There is no doubt that Starship is an incredible and ambitious rocket, but I am wishing for success for both Starship and Neutron. I want to see Starship success because it will enable exploration of the solar system like no other rocket before it. wish for Neutron success because it is frankly a wickedly cool concept and the rocket world needs competition and alternatives. We need companies and people thinking in different ways. Neutron is just one step. If successful, what might Rocket Lab and Peter Beck dream up next time?
Hey, I am even wishing for the success of Blue Origin and the New Glenn. Not because the rocket itself is all that interesting, but because Jeff Bezos has alternative visions for space explorations which are worth pursuing. Bezos wants to build huge space stations people can live in. I think that is cool. It shouldn't be all about Mars colonization. I am greedy: I want it all!
Your calculation on the rocket equation advantage for CF ignores the weight of fuel that must remain for landing. A lighter CF frame also subtracts from the amount of fuel that must be held back, allowing more for payload. This is also a reason it is hard for a hylox first stage to be reusable, the tanks are relatively heavy.